미국 항공우주국(나사·NASA)이 우주 프로젝트에 적용한 3D프린팅 기술 사례를 꾸준히 늘려가고 있다. 나사는 고온, 고압이 발생하는 로켓엔진용 연소실 부품을 3D프린팅 기술로 만들고 실제 발사 조건 실험에서 해당 부품이 본래 모양을 유지하는 데 성공했다.
3D 프린팅 기술전문 매체 3D프린트닷컴은 11일 나사가 앨라배마 주 헌츠빌에 있는 마샬 우주비행센터에서 3D프린팅 기술을 이용해 만든 연소실 부품 검증 실험에 성공했다고 보도했다.
연소실은 실제 발사와 유사한 조건에서 다양한 출력 단계로 20~30초 동안 진행되는 발사 실험을 거쳤다. 최종 발사 실험은 100% 전력으로 25초 동안 이뤄졌다. 실험 완료 후에도 연소실은 제 모양을 유지했다.
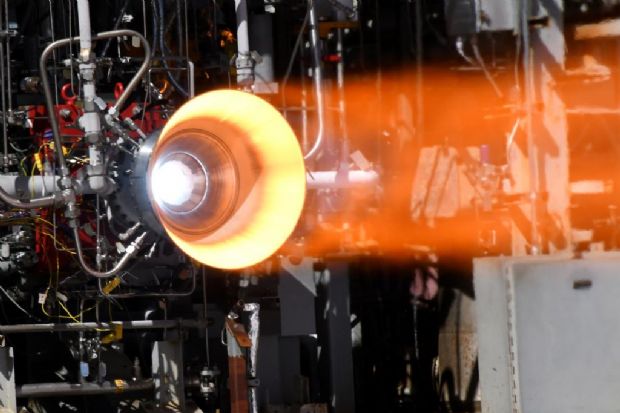
이번 ‘저비용 윗단 추진 프로젝트(The Low Cost Upper Stage-Class Propulsion Project)’ 프로젝트에는 나사와 마샬 우주비행센터 외에도 글렌연구센터와 랭글리연구소가 참여했다.
존 파이크스(John Fikes) 프로젝트 매니저는 “전자빔 자유형 제조 기술(E-Beam Free Form Fabrication)로 만든 연소실 덮개가 내부에서 발생한 압력으로부터 연소실 라이너(chamber liner)를 보호할 수 있다는 것을 입증했다”고 밝혔다.
나사는 앞선 2015년 글렌연구센터의 소재 과학자들이 만든 구리 합금 분말을 이용해 최초의 구리 로켓 엔진 부품인 연소실 라이너를 3D프린터로 제작했다. 랭글리연구소는 전자빔 자유형 제조 기술을 사용해 해당 부품 위에 니켈 합금을 증착시켜 연소실 덮개를 만들었다.
구리 라이너는 열전도성은 좋지만 강도는 떨어진다. 연구원들은 납땜 같은 전통적 공정법을 사용하는 대신 3D프린팅 기술을 활용해 강한 압력을 견딜 수 있는 부품을 만들었다. 이에 따라 수일에서 수주 걸릴 수 있는 작업기간을 몇 시간 내로 줄였다. 부품 자체도 3D프린팅 기술로 제작해 여러 개 부품을 용접할 필요가 없어졌다.
관련기사
- 정부, 3D프린팅 의료기기 제작 상용화 추진2018.05.11
- 국내 발전소 부품, 3D프린팅 기술로 만든다2018.05.11
- GM, 3D프린팅·AI로 자동차 부품 만든다2018.05.11
- 센트롤, 센트롤X로 아트토이컬쳐 2018 참가2018.05.11
나사는 3D프린팅 기술을 활용해 로켓엔진 부품을 만드는 연구를 계속 진행한다.
연소실 덮개와 라이너 제작 기술은 향후 ‘신속한 분석 및 제조 추진 기술(Rapid Analysis and Manufacturing Propulsion Technology)’ 프로젝트에서 다시 연구될 예정이다. 해당 프로젝트는 추력실 모두개(thrust chamber assemblies) 생산 기간과 비용을 줄이는 것이 목표다.