국내 발전소 정비 부품을 3D프린팅 기술로 제작하는 첫 시도가 올해부터 시작된다.
산업통상자원부(산업부)는 9일 시흥시 소재 3D프린팅 제조혁신지원센터에서 국내 발전사 6곳과 함께 국내 발전소 정비부품을 3D프린팅 기술로 제작하는 시범사업 업무협약을 체결했다고 밝혔다.
시범사업에 참여하는 발전소는 한국남동·중부·서부·남부·동서 발전소와 한국수력원자력이다. 한전 전력연구원, 한전 KPS도 사업에 참여한다.
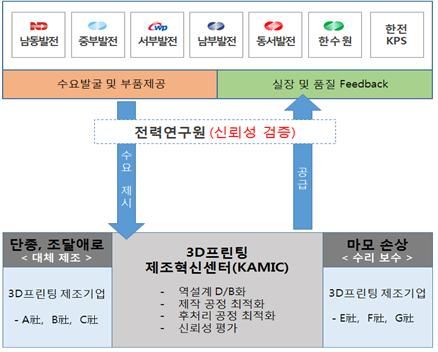
발전소 정비작업에 소요되는 부품을 3D프린팅 기술로 만들어 보는 데 그치지 않고 발전소에서 실제 사용해보는 것까지가 이번 사업의 목표다. 국내 최초 시도기도 하다.
시범사업은 2단계로 이뤄진다. 우선 이달부터 올해 말까지 3D프린터로 제작이 비교적 쉽고 실제 발전소 사용 부담이 적은 2종을 발굴해 시범 제작 후 실장(實裝)을 추진한다. 2단계에선 오는 8월부터 2020년까지 추가 부품 5종에 대한 기술을 개발하고 2021년 3월까지 3D프린팅 기술로 제작해 현장에 적용할 계획이다.
해외에선 이미 발전 분야에 3D프린팅 기술이 이용되고 있다. 제너럴 일렉트릭(GE), 지멘스 같은 글로벌 기업은 가스터빈이나 경수로 핵심부품까지 3D프린팅 기술로 제작해 발전사에 공급하고 있다. 제작기간 50% 단축, 터빈 효율 64% 향상 등 우수한 성과도 거두고 있다.
그러나 국내 발전사는 연구 개발(R&D) 부서 중심으로 3D프린팅 기술을 적용해 손상마모 부품의 보수 가능성을 확인하거나 밸브 같은 일부 소형부품 시제작 시도 정도에 그치고 있다. 국내 발전소의 3D프린팅 기술 이해, 신뢰성이 낮고 고장 우려가 있다 보니 3D프린터로 만든 어떤 부품도 발전소에 실제 사용된 사례가 없는 상황이다.
산업부는 연초부터 이같은 문제 해결을 위해 전국 발전소를 직접 방문해 세미나 등을 통해 3D프린팅 기술을 쉽게 설명하며 근무 인력들을 이해시켰다. 예방정비 기간 동안 해체된 발전소도 직접 들어가 부품들을 일일이 확인하며 3D프린팅 기술로 제작할 수 있는 발전 부품 수요를 발굴하는 등 해법을 찾았다.
이번 시범사업에 3D프린팅 기술에 대한 신뢰성 문제는 한전 전력연구원이 맡는다. 3D프린터로 제조한 부품에 대한 평가, 신뢰성 검증 프로세스를 마련해 발전사에 실제로 사용하는 데 따르는 부담을 최대한 완화시킨다는 계획이다.
관련기사
- GM, 3D프린팅·AI로 자동차 부품 만든다2018.05.09
- 센트롤, 센트롤X로 아트토이컬쳐 2018 참가2018.05.09
- 미국 정부, 에너지 사업에도 3D프린팅 기술 적용2018.05.09
- 센트롤, 저가형 산업용 금속·바인더 3D프린터 출시2018.05.09
고장 우려는 3D프린팅 기술 적용 부품을 적절하게 선택해 해결하기로 했다. 안전과 무관하며 불량이 나도 발전소 가동에 지장이 없고 기존 제작 방법보다 원가 절감이나 효율성은 유리한 듀얼성 부품 등을 선정해 3D프린터로 만든다는 설명이다.
업무 협약식에 참석한 이인호 차관은 “이번 시범사업은 신기술 적용을 가로막는 현장 애로를 합리적으로 해결하면서 기존 제조 방식보다 우월한 부품을 제조할 수 있다는 것을 보여줘 3DP 업체들이 조기에 발전 정비 틈새시장에 진입하도록 하는 데 의의가 있다”고 밝혔다.